In order to save costs and improve economic benefits, advanced production methods such as flexible manufacturing systems and automated warehousing systems have been widely applied. They use highly intelligent systems as the decision-making center and robots, automated three-dimensional warehouses, unmanned handling vehicles, and other main equipment. Among them, forklift type AGVs are highly favored among unmanned handling equipment. They integrate advanced technologies such as electronic computer science, image signal processing, and automatic control, and are key equipment in modern logistics systems and flexible production organization systems
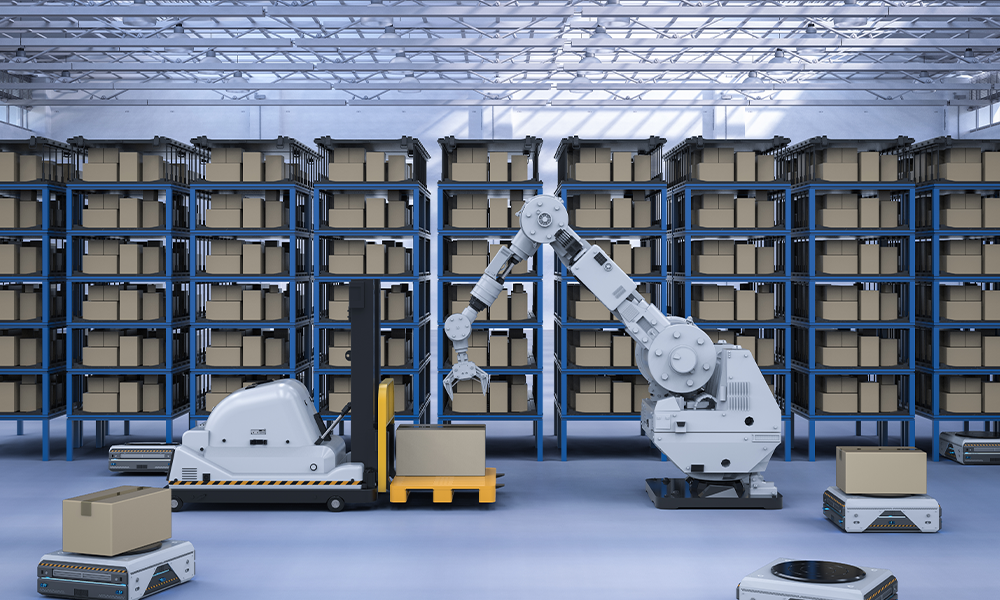
Unmanned forklifts locate products and pick up goods along the optimal path, automatically delivering them to designated workstations. They have been widely used in logistics warehousing and flexible production lines. The application scenarios of unmanned forklifts in the actual transfer of goods are complex, and they will encounter many safety related scenarios. For example, when unmanned forklifts encounter falling goods or other obstacles on their path, if they cannot stop in time, it will cause both parties to be damaged at the same time; When multiple unmanned forklifts are operating simultaneously, it is possible that they may not be able to stop in a timely manner, resulting in collisions with the unmanned forklifts. To enable unmanned forklifts to operate more safely in complex environments, it is necessaryt o obtain information on the presence of static or dynamic obstacles along their route, and to achieve emergency braking or avoid obstacles.
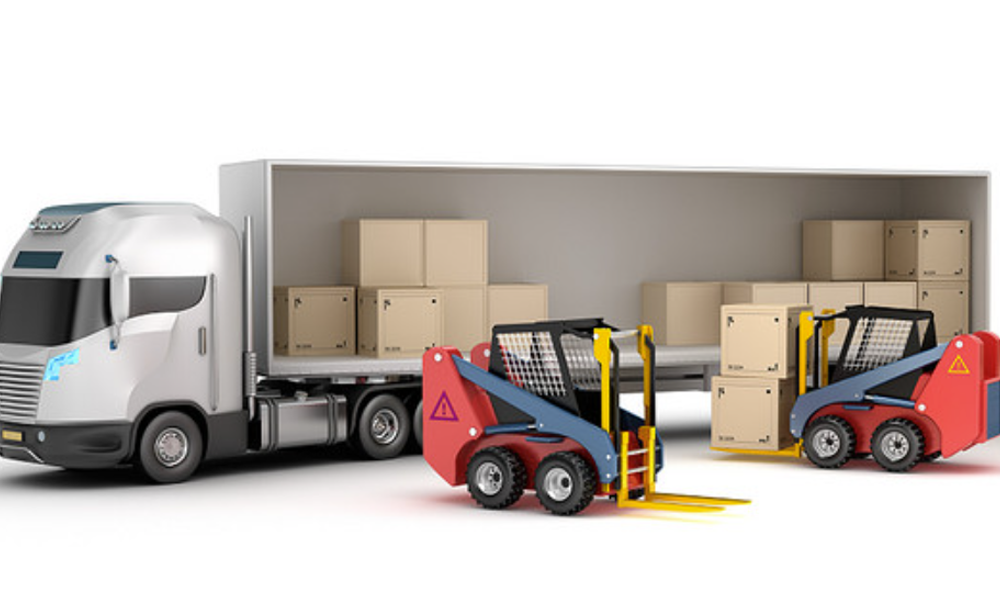
Avoiding obstacles in unknown or partially unknown environments requires real-time acquisition of surrounding environmental information through sensors, including obstacle size, shape, and position. To maximize the accuracy of autonomous obstacle avoidance and positioning navigation for unmanned forklifts in uncertain environments, Laser Eye provides various models of LiDAR, which can improve the accuracy of autonomous positioning, fork tip positioning, and obstacle avoidance for unmanned forklifts, thereby achieving automatic handling of warehouse goods in complex scenarios.
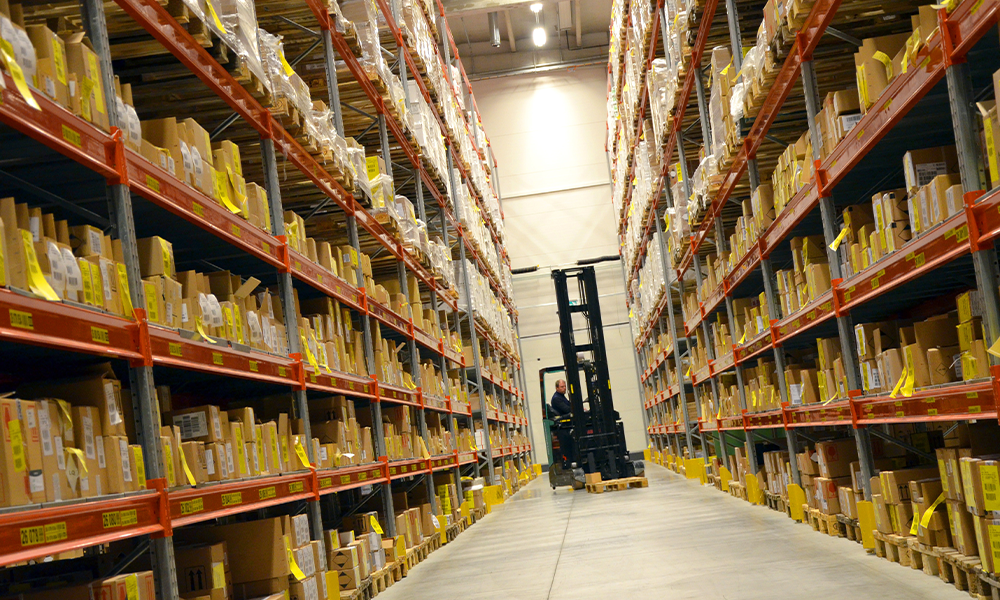
ILS-N70 high-precision navigation obstacle avoidance lidar
It is based on the laser time flight method to measure the distance between the object being measured, with characteristics such as high precision, high resolution, and high scanning frequency. It has navigation point cloud data output function and obstacle avoidance algorithm, which can enable AGV robots to adapt to flexible and changing work locations, achieve precise material retrieval and placement, and enable flexible intelligent manufacturing, assisting in ultra efficient operations.
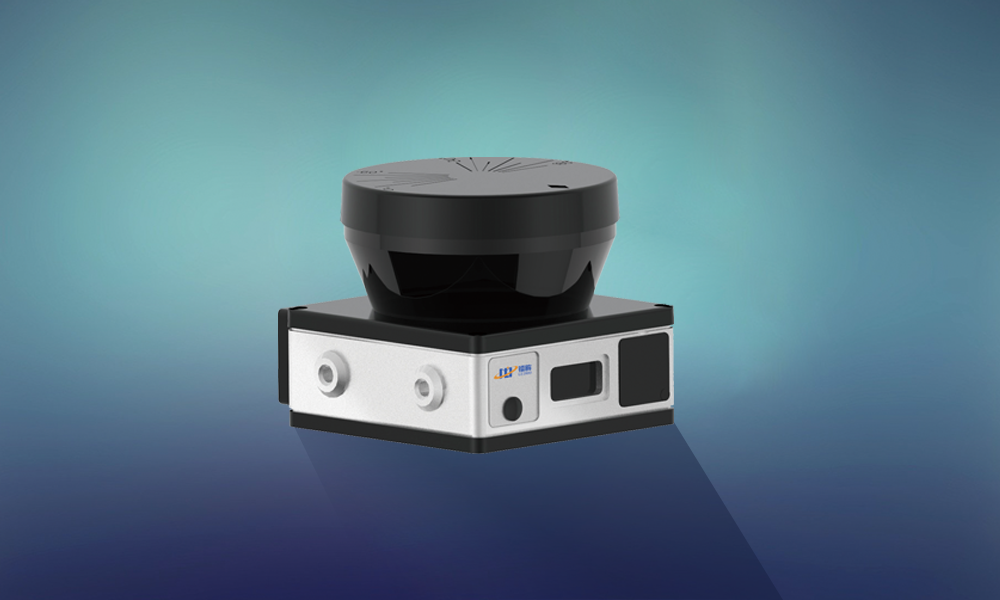
Product features
16 switchable area groups, with a maximum of 8 synchronized monitoring areas within each area group
300 ° ultra large field of view, safety protection is effortless
Adjustable scanning frequency, up to 30Hz
Adjustable angle resolution, up to a minimum of 0.09 °
Measurement accuracy within ± 1cm, ensuring stable operation of equipment
ILS-T52 3D imaging lidar
T52 is a high-performance pure solid-state LiDAR that uses laser time flight method to provide excellent 3D image imaging and depth sensing functions. Especially suitable for the field of unmanned forklifts, providing excellent 3D imaging and depth sensing functions for obstacle avoidance at the fork tip. Its high precision, adaptive automatic exposure, small size, low power consumption, and high-resolution output characteristics help unmanned forklifts improve operational safety and efficiency, ensure smooth operation and precise fork tip obstacle avoidance, and make forklift operations more intelligent, safe, and reliable.
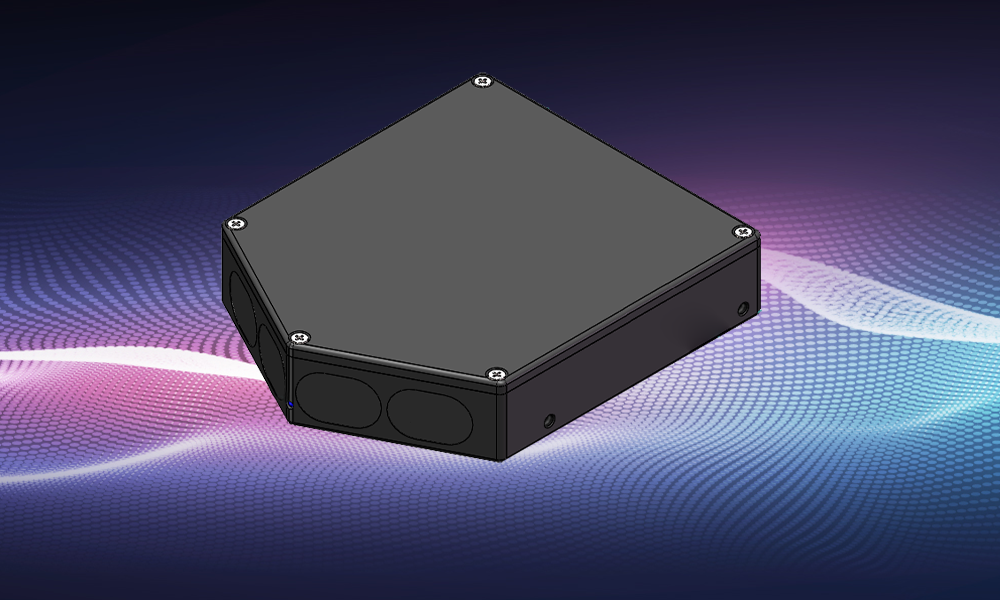
Product features
3D imaging, capable of simultaneously outputting depth and IR point cloud data
The maximum image resolution can reach 640x240 (adjustable)
The maximum field of view range can reach 120 ° x55 ° (± 3 ° error)
2cm ultra-thin body design, suitable for most AGV/AMR models
Commonly used for AGV navigation and obstacle avoidance, forklift end alignment and obstacle avoidance, and other scenarios